In-House PVD Coating Capabilities
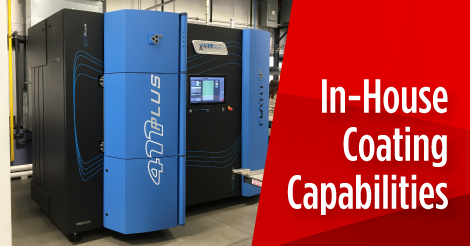
This month we're talking about our coating capabilities and efficiencies, and how these factors ultimately contribute to greater tool life and value to the customer. I spoke with our Supply Chain Manager, John Sheehan, to get the full run-down on all things coating-related. A little about John, he has been part of the Fullerton team for almost 8 years and manages purchasing, media hone, post polish operations, cleaning, as well as the coating center. John is no stranger to the cutting tool industry, with over 39 years of industry experience. He has compiled a strong team of individuals who are a major asset in supporting the end of our tools journey before they go to the customer. This team is a versatile group who are crossed trained to step in at any given moment and any given position to move the product and meet customer expectations. That is just one of the many reasons why our coating capabilities are top-notch.
Here at Fullerton, we use a PVD coating process. PVD is a plasma coating process that involves the depositing of thin solid layers of another material onto a surface or part to make that object more durable. Our PVD plating adds a lightweight, yet solid, layer of protection which aids the tool in many ways. There of course are other reasons why coatings add value to cutting tools, check out some of the reasons below.
- Additional Hardness - As the coating makes the tool surface layer material harder. A more durable cutting edge will enhance the device's performance as there is less chance of wear thru abrasion. With this a tool will maintain its edge retention, keeping it sharper for longer.
- Lubricity - Coatings also add an additional surface lubricity to the cutting faces, reducing build-up, adhesion, and galling, promoting chip flow, and increasing machining efficiencies and tool functionality.
- Heat Resistance - Coatings offer a substantial benefit with the addition of a thermal barrier between the workpiece and cutting tool, allowing increased cutting parameters and efficiencies to the operations.
- Differentiation - Tools can be plated using different colored PVD coating material. Which can help differentiate identical tools designating a rougher from a finisher or regrind from new.
We offer a variety of coatings on our carbide cutting tools. Here at Fullerton, we currently coat approximately 87% of our coatings in-house, with nearly 3,000 tools per day. Our diverse experience throughout our entire coating team is second to none in controlling logistics and holding a standard of quality above and beyond any outside vendor-supplied coatings. Our constant research and testing keep Fullerton on the "cutting edge" of new coatings and processes.
You can learn more about our more popular coatings at https://fullertontool.com/resources/education or find out what coating is best for your material and operation at https://fullertontool.com/resources/coating-search.
Have more questions or want more information? Contact your dedicated Fullerton Direct Sales Representative (which you can find at https://fullertontool.com/contact/locator) on how our in-house coating center can add convenience and value to you.