Chip control in milling is an ongoing challenge; issues like chip wrap, recutting, and evacuation have troubled the industry since its inception. With the rapid advancements in High-Efficiency Machining (HEM), these issues have become even more pronounced. Effective chip evacuation relies heavily on the available space around the cutting tool. An increased number of flutes, longer work engagement, and greater chip loads diminish the space needed to expel the removed material.
To address these problems, controlling the size and direction of waste is essential, as it promotes better flute clearance and evacuation. However, implementing efficient chip control presents challenges. First, it is crucial that chip control methods do not negatively affect the surface finish of the part being machined. Second, for every conventional chip breaker added along the cutting edge, there is an increase in stress and load on the tooth behind it. Finally, adding chip breakers reduces the cutting edge length of the flute by the width of each notch multiplied by the number of notches present.
To address the critical importance of chip removal and the potential issues it can cause in manufacturing processes, Fullerton has developed the revolutionary "Chip Splitter" technology. This innovative design not only enhances chip management but also brings significant mechanical advantages and engineering improvements over traditional chip breakers available on the market.
Chip Splitter Key Features
- Minimizes stress risers in the flute while balancing cutting forces along the cutting edge.
- Enhances chip flow and evacuation.
- Controls chip formation, contributing to a better surface finish on the machined part.
- Reduces spindle load and cutting resistance, leading to lower cutting forces, improved efficiency in today's HEM machining, longer tool life, and reduced risk of tool breakage.
- Frees up the tool during cutting to reduce vibration and chatter, minimizing distortion in the workplace.
- Decreases chip recutting in challenging aerospace materials.
- Prevents chip entanglement in the cutter body to facilitate efficient chip evacuation.
- Promotes efficient chip disposal and handling by breaking long, continuous chips into smaller, more manageable pieces, which improves cutting efficiency.
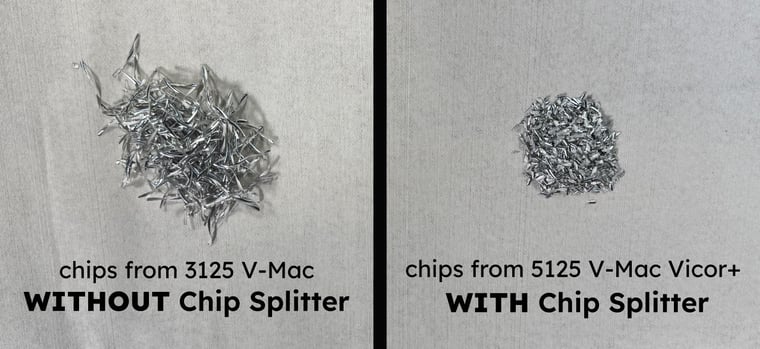
V-Mac Vicor+ With Chip Splitters
Consider the chip splitter - another innovative advancement in our successful 5125 V-Mac Vicor+ series. This feature enhances the performance and efficiency of cutting tools. By breaking up chips and improving chip control, chip splitters can help increase productivity, extend tool life, and enhance safety. Check out the difference chip splitters made in the above picture when we put the 3125 V-Mac head-to-head with the 5125 V-Mac Vicor+. The results speak for themselves, showcasing superior performance and efficiency.
Learn more about how the V-Mac Vicor+ can revolutionize your manufacturing processes.