Aluminum is one of the most used materials in modern manufacturing due to its lightweight and high strength-to-weight ratio. However, machining aluminum can present several challenges, such as chip buildup, poor surface finish, and premature tool wear. In this article, we will discuss why machining aluminum can be difficult and explore end mills that excel across aluminum applications, providing a solution to many of the challenges associated with machining this versatile material.
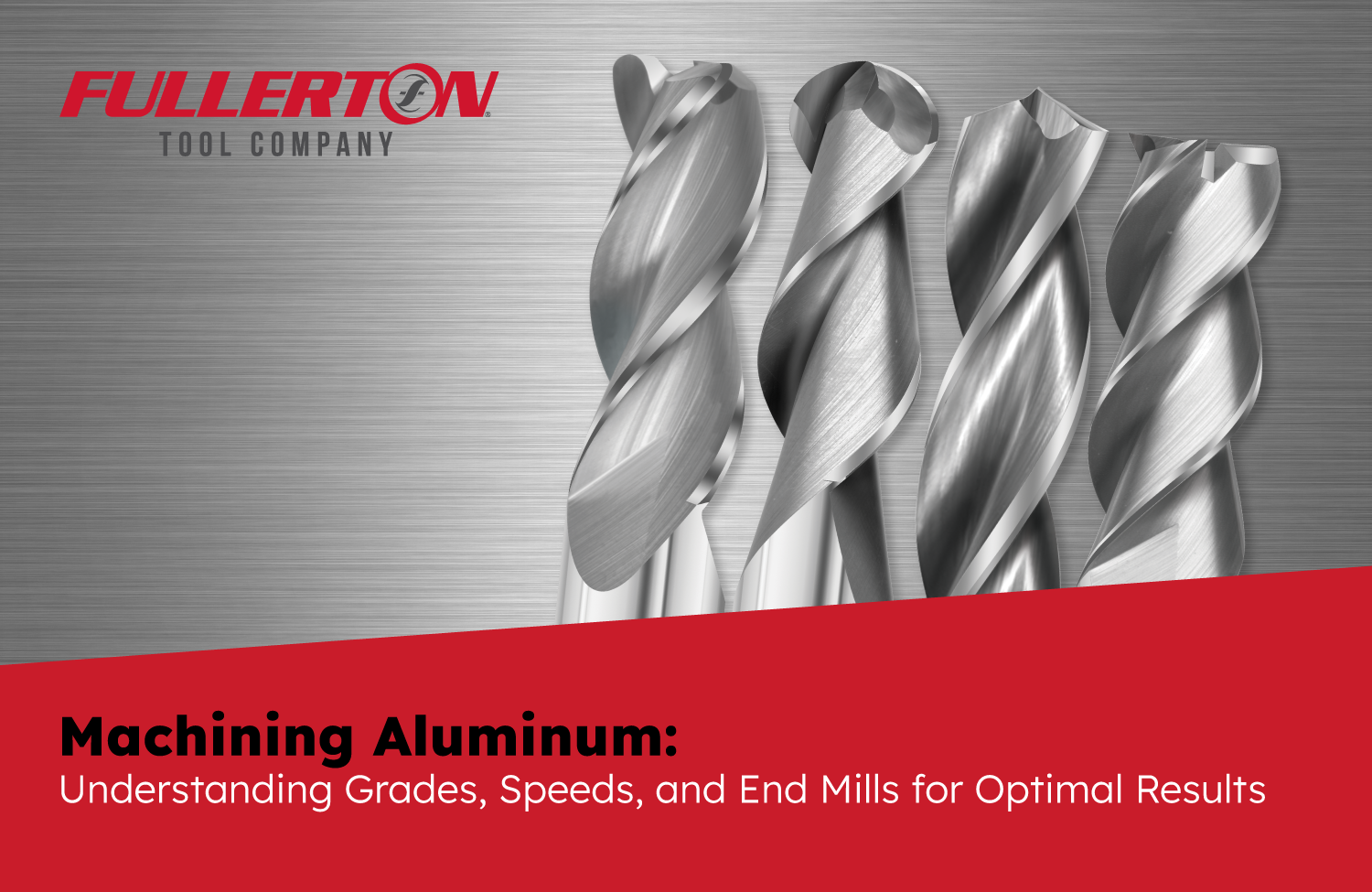
Challenges with Machining in Aluminum
Machining aluminum can be challenging for several reasons, check out the reasons below.
- Adhesion: Aluminum tends to build or accumulate material on the cutting edge, which can cause the tool to become clogged and reduce its cutting performance and cause premature breakage. High-polished cutting edges or tool coatings can greatly reduce adhesion and promote tool life and surface finish.
- Chip Formation: Aluminum tends to produce long, stringy chips that can wrap around the cutting tool, causing it to become clogged and reducing its cutting performance. Chip breakers are commonly employed for chip control and aid in clearing the chip quickly.
- Tool Material: The choice of tool material is important for machining aluminum, and not all grades are equally effective. For example, some tool materials are more prone to wear or breakage than others when machining aluminum. Cobalt content and grain structure can affect tool life greatly.
Due to these factors, machining aluminum with cutting tools requires careful selection of the cutting tool, cutting parameters, and machine conditions to ensure optimal cutting performance and tool life. Find out more about the different grades of aluminum, and recommended surface feed per minute (SFM) rates based on the aluminum grade.
Grades of Aluminum
There are many different grades of aluminum, each with its own unique set of properties and characteristics that can affect the machining process. Some common grades of aluminum include:
- 1xxx Series: A popular choice for a wide range of applications, 1100 aluminum is commercially pure aluminum and is known for being soft and ductile with excellent formability and low strength. It is nonheat treatable.
Recommended SFM = > 2,300
- 2xxx Series: High-strength aluminum alloy, 2024 is commonly used in aerospace applications. Copper is the primary alloying element in the 2000 series family. When heat-treated, these alloys have mechanical properties equivalent to mild steel.
Recommended SFM = > 800
- 5xxx Series: A medium-strength aluminum alloy, 5052 is often used in marine and automotive applications. Because this is so soft, it's usually used for forming applications. It's one of the stickier grades, so it can tend to heat up quickly and lead to flute and cutting-edge buildup.
Recommended SFM = > 1,600
- 6xxx Series: A popular choice for a wide range of applications, 6061 aluminum is a heat-treatable aluminum alloy containing silicon and magnesium with good corrosion resistance and excellent mechanical properties. These alloys have been machinability compared with the 2xxx series at the expense of lower strength.
Recommended SFM = > 2,000
- 7xxx Series: This high-strength aluminum alloy, 7075 is often used in aerospace, marine, and defense applications. Its main alloying element is zinc but also contains copper, chromium, and magnesium.
Recommended SFM = > 1,800 (you can use higher SFM when machining these types of materials, but you must use light RDoC and control the feed rates)
Aluminum End Mill Solutions
Check out our recommend AlumaMill series end mills that excel across all your aluminum applications, providing a comprehensive solution to the challenges associated with machining this popular material.

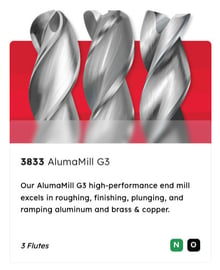
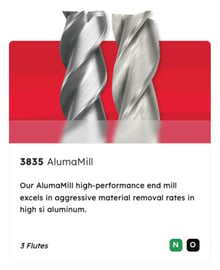