Aluminum is a widely used material known for its machinability and versatility. To achieve precision and efficiency in aluminum, selecting the appropriate end mills is crucial. Among the various types of end mills available, the 2-flute and 3-flute end mills stand out as the most popular choices. Although there are non-ferrous cutters out there with teeth counts greater than 3, most of these can only be used with the fastest of controllers or larger parts allowing controllers to reach optimization.
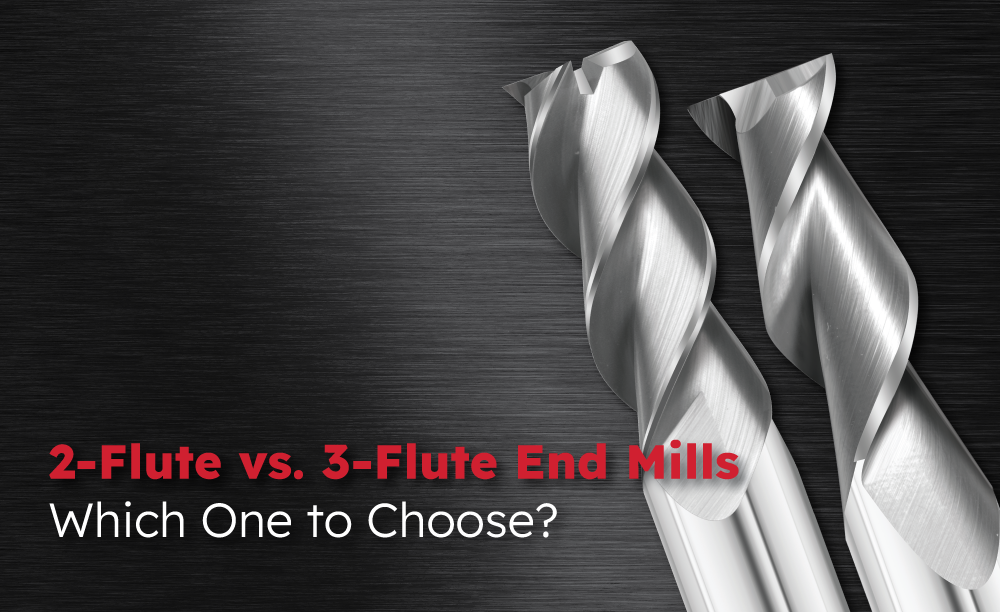
In this article, we will delve into the characteristics and applications of both end mill types, helping you make an informed decision on flute count when machining in aluminum.
Choosing between 2-flute versus 3-flute end mills when machining in aluminum depends on several factors, including the specific operation being performed, the desired surface finish, and the machine’s capabilities. The depth of cut and radial engagement will also affect the flute count, in terms of tool pressure from increased points of contact along the cutting edge.
2-Flute End Mills
A 2-flute end mill features two cutting edges (flutes) and provides ample space for chip evacuation. The larger flute space allows for increased radial engagement and chip loads making it well-suited for aggressive material removal.
When to Use a 2-Flute End Mill?
- High Material Removal Rates: When your priority is to remove large volumes of aluminum quickly, a 2-flute end mill is your ideal choice. The increased chip space and aggressive cutting action facilitate rapid stock removal, increasing the tools’ ability to clear chips effectively.
- Low-Power Machines: If you’re using a low-power milling machine or a machine fixturing with limited rigidity, a 2-flute end mill can be beneficial because its design puts less strain on the machine.
- Deep Depth of Cuts or Long Sidewall Consideration: Fewer points of contact will provide less radial push-off and reduce wall taper significantly when paired with optimized helix angles.
3-Flute End Mills
A 3-flute end mill comes with three cutting edges (flutes), making it more versatile in certain scenarios. The additional flute provides an easier transition from flute to flute, changing the characteristics of the surface finish.
When to Use a 3-Flute End Mill?
- Finishing Operations: For achieving exceptional surface finishes, a 3-flute end mill is more suitable due to reduced radial forces. The lower radial forces minimize the risk of part deformation and ensure higher machining accuracy.
- Chip Evacuation is a Concern: Three flute end mills offer an excellent balance between chip removal and surface finish. It is especially useful in scenarios where chip evacuation might be a concern, but smooth surface finishes are still essential.
- Roughing: A 3-flute end mill provides increased stability and reduces the radial forces acting on the tool, resulting in better surface finishes and improved tool life. However, they remove material more slowly than 2-flute end mills, but the balance between lighter feed rate with the additional flute will often benefit the user.
In conclusion, the choice between a 2-flute and 3-flute end mill when machining in aluminum depends on the specific requirements of your project. Ultimately, the best way to choose the right end mill when machining in aluminum is to work directly with our Sales or Engineering teams. They will help you assess your specific needs and recommend the right tool for your application.