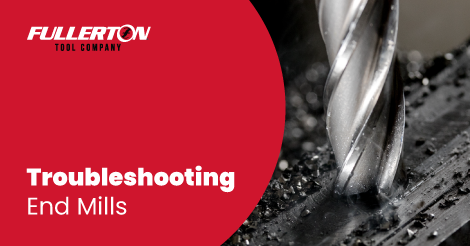
Modern programming methods, upgraded materials, and advanced cutting tools have helped extend the cutting tool lifespan despite the ever-increasing workload they are exposed to. Skilled users should be aware of the most frequent causes of premature carbide failures and should acquire the skills to recognize and correct minor problems. We will discuss common causes and solutions you may face in applying carbide tooling.
The following table lists some of the common problems encountered in machining operations. While it can be very helpful in identifying the source of many problems, keep in mind our applications and engineering teams will always be available to help you optimize your cutting tools.
End Mill Troubleshooting Guide
Issue |
Cause |
Solution |
Tool Break |
Feed Rate Excessive |
Increase SFM |
Depth of Cut Excessive |
Reduce Depth of Cut |
Excessive Tool Overhang |
Reduce Tool Stick Out |
Excessive Tool Wear |
Regrind Sooner |
Excessive Wear |
Speed Is Too Fast |
Decrease Speed |
Hard Work Material |
Change Coating |
Wrong Speed/Feed |
Increase Speed/Feed |
Primary Relief Angle Too Low |
Change to Larger Relief Angle |
Recutting Chips |
Change Feed/Speed/Increase Coolant |
Poor Surface Finish |
Feed Rate Too Fast |
Correct Feed/Speed Rates |
Cutting Speed Too Slow |
Increase RPM |
Recutting Chips |
Change Feed/Speed/Increase Coolant |
Excessive Wear |
Regrind Sooner |
Tool Runout |
Check Tool Runout in Holder/Spindle, <.0003 TIR Desired |
Excessive Tool Overhang |
Reduce Tool Stick Out Reduce SFM/Increase IPT |
Chip Packing |
Cut Too Heavy |
Decrease Depth and Width of Cut |
Minimal Chip Clearance |
End Mill with Fewer Flutes |
Lack of Coolant |
Higher Coolant Pressure/Reposition Nozzle |
Want more technical information on our end mills? Check out our Technical Guide - End Mills at https://fullertontool.com/media/Fullerton-Technical-Guide.pdf